Κωδικός QR
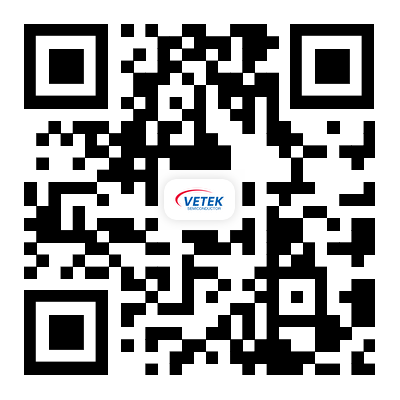
Σχετικά με εμάς
Προϊόντα
Επικοινωνήστε μαζί μας
Τηλέφωνο
Φαξ
+86-579-87223657
ΗΛΕΚΤΡΟΝΙΚΗ ΔΙΕΥΘΥΝΣΗ
Διεύθυνση
Wangda Road, οδός Ziyang, κομητεία Wuyi, πόλη Jinhua, επαρχία Zhejiang, Κίνα
Η κατασκευή κάθε προϊόντος ημιαγωγών απαιτεί εκατοντάδες διαδικασίες και ολόκληρη η διαδικασία παραγωγής χωρίζεται σε οκτώ βήματα:Επεξεργασία πλακιδίων - Οξείδωση - Φωτολιθογραφία - Χάραξη - εναπόθεση λεπτού φιλμ - διασύνδεση - Δοκιμές - Συσκευασία.
Βήμα 5: εναπόθεση λεπτού φιλμ
Προκειμένου να δημιουργηθούν οι μικροεπιστημές μέσα στο τσιπ, πρέπει να καταθέσουμε συνεχώς στρώματα λεπτών μεμβρανών και να αφαιρέσουμε τα περίσσεια εξαρτήματα με χάραξη και επίσης να προσθέσουμε κάποια υλικά για να χωριστούν διαφορετικές συσκευές. Κάθε τρανζίστορ ή κελί μνήμης είναι κατασκευασμένο βήμα προς βήμα μέσα από την παραπάνω διαδικασία. Η "λεπτή μεμβράνη" για την οποία μιλάμε εδώ αναφέρεται σε μια "ταινία" με πάχος μικρότερο από 1 micron (μm, ένα εκατομμύριο ενός μετρητή) που δεν μπορεί να κατασκευαστεί με συνήθεις μεθόδους μηχανικής επεξεργασίας. Η διαδικασία τοποθέτησης μιας μεμβράνης που περιέχει τις απαιτούμενες μοριακές ή ατομικές μονάδες σε ένα δίσκο είναι "εναπόθεση".
Για να σχηματίσουμε μια δομή ημιαγωγών πολλαπλών στρώσεων, πρέπει πρώτα να κάνουμε μια στοίβα συσκευής, δηλαδή, εναλλάξ στοίβα πολλαπλές στρώσεις λεπτών μεταλλικών (αγώγιμων) μεμβράνων και διηλεκτρικών (μονωτικών) μεμβράνων στην επιφάνεια του δίσκου και στη συνέχεια να αφαιρέσουν τα περίσσεια μέρη μέσω επαναλαμβανόμενων διαδικασιών χάραξης για να σχηματίσουν μια τρισδιάστατη δομή. Οι τεχνικές που μπορούν να χρησιμοποιηθούν για τις διαδικασίες εναπόθεσης περιλαμβάνουν χημική εναπόθεση ατμών (CVD), εναπόθεση ατομικής στρώσης (ALD) και απόθεση φυσικής ατμών (PVD) και μεθόδους που χρησιμοποιούν αυτές τις τεχνικές μπορούν να χωριστούν σε ξηρή και υγρή εναπόθεση.
Χημική εναπόθεση ατμών (CVD)
Στην εναπόθεση χημικών ατμών, τα πρόδρομα αέρια αντιδρούν σε ένα θάλαμο αντίδρασης για να σχηματίσουν ένα λεπτό φιλμ που συνδέεται με την επιφάνεια του δισκίου και των υποπροϊόντων που αντλούνται από το θάλαμο. Η ενισχυμένη με πλάσμα χημική εναπόθεση ατμών χρησιμοποιεί πλάσμα για τη δημιουργία των αερίων αντιδραστηρίου. Αυτή η μέθοδος μειώνει τη θερμοκρασία αντίδρασης, καθιστώντας την ιδανική για δομές ευαίσθητες στη θερμοκρασία. Η χρήση του πλάσματος μπορεί επίσης να μειώσει τον αριθμό των καταθέσεων, συχνά με αποτέλεσμα ταινίες υψηλότερης ποιότητας.
Ατομική εναπόθεση στρώματος (ALD)
Η εναπόθεση ατομικού στρώματος σχηματίζει λεπτές μεμβράνες εναπόθεσης μόνο μερικών ατομικών στρωμάτων κάθε φορά. Το κλειδί αυτής της μεθόδου είναι να κυκλοφορούν ανεξάρτητα βήματα που εκτελούνται με μια συγκεκριμένη σειρά και να διατηρούν καλό έλεγχο. Η επικάλυψη της επιφάνειας του δίσκου με έναν πρόδρομο είναι το πρώτο βήμα και στη συνέχεια εισάγονται διαφορετικά αέρια για να αντιδράσουν με τον πρόδρομο για να σχηματίσουν την επιθυμητή ουσία στην επιφάνεια του δίσκου.
Φυσική εναπόθεση ατμών (PVD)
Όπως υποδηλώνει το όνομα, η απόθεση φυσικής ατμών αναφέρεται στον σχηματισμό λεπτών μεμβρανών με φυσικά μέσα. Το Sputtering είναι μια μέθοδος φυσικής εναπόθεσης ατμών που χρησιμοποιεί πλάσμα αργού για να ψεκαστεί άτομα από ένα στόχο και να τα καταθέσει στην επιφάνεια ενός δισκίου για να σχηματίσει ένα λεπτό φιλμ. Σε ορισμένες περιπτώσεις, η μεμβράνη που έχει κατατεθεί μπορεί να αντιμετωπιστεί και να βελτιωθεί μέσω τεχνικών όπως η υπεριώδη θερμική επεξεργασία (UVTP).
Βήμα 6: διασύνδεση
Η αγωγιμότητα των ημιαγωγών είναι μεταξύ των αγωγών και των μη αγωγών (δηλαδή των μονωτήρων), που μας επιτρέπει να ελέγξουμε πλήρως τη ροή της ηλεκτρικής ενέργειας. Οι διαδικασίες λιθογραφίας, χάραξης και εναπόθεσης με βάση το πλακίδιο μπορούν να δημιουργήσουν εξαρτήματα όπως τρανζίστορ, αλλά πρέπει να συνδεθούν για να επιτρέψουν τη μετάδοση και την λήψη ισχύος και σημάτων.
Τα μέταλλα χρησιμοποιούνται για διασύνδεση κυκλώματος λόγω της αγωγιμότητας τους. Τα μέταλλα που χρησιμοποιούνται για τους ημιαγωγούς πρέπει να πληρούν τις ακόλουθες προϋποθέσεις:
· Χαμηλή αντίσταση: Δεδομένου ότι τα μεταλλικά κυκλώματα πρέπει να περάσουν το ρεύμα, τα μέταλλα σε αυτά θα πρέπει να έχουν χαμηλή αντίσταση.
· Θερμοχημική σταθερότητα: Οι ιδιότητες των μεταλλικών υλικών πρέπει να παραμείνουν αμετάβλητες κατά τη διάρκεια της διαδικασίας μετάλλων.
· Υψηλή αξιοπιστία: Καθώς αναπτύσσεται η ενσωματωμένη τεχνολογία κυκλώματος, ακόμη και οι μικρές ποσότητες υλικών διασύνδεσης μετάλλων πρέπει να έχουν επαρκή ανθεκτικότητα.
· Κόστος κατασκευής: Ακόμη και αν πληρούνται οι τρεις πρώτες προϋποθέσεις, το κόστος υλικού είναι πολύ υψηλό για να καλύψει τις ανάγκες της μαζικής παραγωγής.
Η διαδικασία διασύνδεσης χρησιμοποιεί κυρίως δύο υλικά, αλουμίνιο και χαλκό.
Διαδικασία διασύνδεσης αλουμινίου
Η διαδικασία διασύνδεσης αλουμινίου αρχίζει με εναπόθεση αλουμινίου, εφαρμογή φωτοανθεραπείας, έκθεση και ανάπτυξη, ακολουθούμενη από τη χάραξη για να αφαιρέσει επιλεκτικά τυχόν υπερβολική αλουμινίου και φωτοανθεραπεία πριν εισέλθει στη διαδικασία οξείδωσης. Αφού ολοκληρωθούν τα παραπάνω βήματα, επαναλαμβάνονται οι διαδικασίες φωτοβολιτογραφίας, χάραξης και εναπόθεσης μέχρι να ολοκληρωθεί η διασύνδεση.
Εκτός από την εξαιρετική αγωγιμότητά του, το αλουμίνιο είναι επίσης εύκολο στην φωτοθεογραφία, τη χάραξη και την κατάθεση. Επιπλέον, έχει χαμηλό κόστος και καλή πρόσφυση στο μεμβράνη οξειδίου. Τα μειονεκτήματά του είναι ότι είναι εύκολο να διαβρωθεί και έχει χαμηλό σημείο τήξης. Επιπλέον, για να αποφευχθεί η αντίδραση του αλουμινίου με πυρίτιο και προκαλώντας προβλήματα σύνδεσης, πρέπει να προστεθούν μεταλλικές αποθέσεις σε ξεχωριστό αλουμίνιο από το δίσκο. Αυτή η κατάθεση ονομάζεται "Barrier Metal".
Τα κυκλώματα αλουμινίου σχηματίζονται με εναπόθεση. Αφού εισέλθει στο θάλαμο κενού, ένα λεπτό φιλμ που σχηματίζεται από σωματίδια αλουμινίου θα προσκολληθεί στο δίσκο. Αυτή η διαδικασία ονομάζεται "εναπόθεση ατμών (VD)", η οποία περιλαμβάνει την εναπόθεση χημικών ατμών και την απόθεση φυσικής ατμών.
Διαδικασία διασύνδεσης χαλκού
Καθώς οι διεργασίες ημιαγωγών γίνονται πιο εξελιγμένες και τα μεγέθη των συσκευών συρρικνώνονται, η ταχύτητα σύνδεσης και οι ηλεκτρικές ιδιότητες των κυκλωμάτων αλουμινίου δεν είναι πλέον επαρκείς και απαιτούνται νέοι αγωγοί που πληρούν τόσο τις απαιτήσεις μεγέθους όσο και κόστους. Ο πρώτος λόγος που ο χαλκός μπορεί να αντικαταστήσει το αλουμίνιο είναι ότι έχει χαμηλότερη αντίσταση, η οποία επιτρέπει ταχύτερες ταχύτητες σύνδεσης συσκευής. Ο χαλκός είναι επίσης πιο αξιόπιστος, επειδή είναι πιο ανθεκτικό στην ηλεκτρομανοποίηση, την κίνηση των μεταλλικών ιόντων όταν το ρεύμα ρέει μέσα από ένα μέταλλο, από το αλουμίνιο.
Ωστόσο, ο χαλκός δεν σχηματίζει εύκολα ενώσεις, καθιστώντας δύσκολη την εξατομικευμένη και απομάκρυνση από την επιφάνεια ενός δισκίου. Για να αντιμετωπιστούν αυτό το πρόβλημα, αντί να χάραξε χαλκό, καταθέτουμε τα διηλεκτρικά υλικά, τα οποία σχηματίζουν μεταλλικά πρότυπα που αποτελούνται από τάφρους και βήματα όπου χρειάζεται και στη συνέχεια γεμίζουν τα προαναφερθέντα "μοτίβα" με χαλκό για να επιτύχουμε τη διασύνδεση, μια διαδικασία που ονομάζεται "Δαμασκένιο".
Καθώς τα άτομα χαλκού συνεχίζουν να διαχέονται στο διηλεκτρικό, η μόνωση του τελευταίου μειώνεται και δημιουργεί ένα στρώμα φραγμού που εμποδίζει τα άτομα χαλκού από περαιτέρω διάχυση. Στη συνέχεια σχηματίζεται ένα λεπτό στρώμα σπόρου χαλκού στο στρώμα φραγμού. Αυτό το βήμα επιτρέπει την ηλεκτρολυτική, η οποία είναι η πλήρωση των υψηλών μοτίβων αναλογίας διαστάσεων με χαλκό. Μετά την πλήρωση, η περίσσεια χαλκού μπορεί να αφαιρεθεί με μεταλλική χημική μηχανική στίλβωση (CMP). Μετά την ολοκλήρωση, μπορεί να κατατεθεί ένα μεμβράνη οξειδίου και η περίσσεια μεμβράνη μπορεί να αφαιρεθεί με τη φωτοβολιτογραφία και τις διαδικασίες χάραξης. Η παραπάνω διαδικασία πρέπει να επαναληφθεί μέχρι να ολοκληρωθεί η διασύνδεση χαλκού.
Από την παραπάνω σύγκριση, μπορεί να φανεί ότι η διαφορά μεταξύ της διασύνδεσης χαλκού και της διασύνδεσης αλουμινίου είναι ότι η περίσσεια χαλκού απομακρύνεται από το μεταλλικό CMP και όχι με τη χάραξη.
Βήμα 7: Δοκιμές
Ο κύριος στόχος της δοκιμής είναι να επαληθευτεί εάν η ποιότητα του τσιπ ημιαγωγών πληροί ένα συγκεκριμένο πρότυπο, ώστε να εξαλείψει τα ελαττωματικά προϊόντα και να βελτιωθεί η αξιοπιστία του τσιπ. Επιπλέον, τα ελαττωματικά προϊόντα που δοκιμάζονται δεν θα εισέλθουν στο βήμα συσκευασίας, το οποίο βοηθά στην εξοικονόμηση κόστους και χρόνου. Η ηλεκτρονική διαλογή της μήτρας (EDS) είναι μια μέθοδος δοκιμής για τα πλακίδια.
Το EDS είναι μια διαδικασία που επαληθεύει τα ηλεκτρικά χαρακτηριστικά κάθε τσιπ στην κατάσταση των πλακιδίων και έτσι βελτιώνει την απόδοση ημιαγωγών. Τα ED μπορούν να χωριστούν σε πέντε βήματα, ως εξής:
01 Ηλεκτρική παρακολούθηση παραμέτρων (EPM)
Το EPM είναι το πρώτο βήμα στη δοκιμή τσιπ ημιαγωγών. Αυτό το βήμα θα δοκιμάσει κάθε συσκευή (συμπεριλαμβανομένων των τρανζίστορ, των πυκνωτών και των δίοδοι) που απαιτούνται για τα ολοκληρωμένα κυκλώματα ημιαγωγών για να εξασφαλιστεί ότι οι ηλεκτρικές παραμέτρους τους πληρούν τα πρότυπα. Η κύρια λειτουργία του EPM είναι η παροχή μετρημένων ηλεκτρικών χαρακτηριστικών δεδομένων, τα οποία θα χρησιμοποιηθούν για τη βελτίωση της αποτελεσματικότητας των διαδικασιών παραγωγής ημιαγωγών και της απόδοσης του προϊόντος (όχι για την ανίχνευση ελαττωματικών προϊόντων).
02 δοκιμή γήρανσης
Ο ρυθμός ελαττωμάτων ημιαγωγού προέρχεται από δύο πτυχές, δηλαδή τον ρυθμό παραγωγής ελαττωμάτων (υψηλότερο στο αρχικό στάδιο) και το ρυθμό των ελαττωμάτων σε ολόκληρο τον κύκλο ζωής. Η δοκιμή γήρανσης των πλακιδίων αναφέρεται στη δοκιμή του δισκίου κάτω από μια ορισμένη τάση θερμοκρασίας και AC/DC για να διαπιστωθεί τα προϊόντα που μπορεί να έχουν ελαττώματα στο πρώιμο στάδιο, δηλαδή να βελτιωθεί η αξιοπιστία του τελικού προϊόντος ανακαλύπτοντας πιθανά ελαττώματα.
03 Ανίχνευση
Μετά την ολοκλήρωση της δοκιμής γήρανσης, το τσιπ ημιαγωγών πρέπει να συνδεθεί με τη συσκευή δοκιμής με κάρτα ανιχνευτή και στη συνέχεια μπορούν να πραγματοποιηθούν δοκιμές θερμοκρασίας, ταχύτητας και κίνησης στο δίσκο για την επαλήθευση των σχετικών λειτουργιών ημιαγωγού. Ανατρέξτε στον πίνακα για μια περιγραφή των συγκεκριμένων βημάτων δοκιμής.
04 Επισκευή
Η επισκευή είναι το πιο σημαντικό δοκιμαστικό βήμα, επειδή ορισμένες ελαττωματικές μάρκες μπορούν να επισκευαστούν αντικαθιστώντας τα προβληματικά συστατικά.
05 Dotting
Τα τσιπ που απέτυχαν στην ηλεκτρική δοκιμή έχουν διευθετηθεί στα προηγούμενα βήματα, αλλά πρέπει να επισημανθούν για να τα διακρίνουν. Στο παρελθόν, έπρεπε να επισημάνουμε ελαττωματικά τσιπ με ειδικό μελάνι για να διασφαλίσουμε ότι θα μπορούσαν να ταυτοποιηθούν με το γυμνό μάτι, αλλά τώρα το σύστημα τα ταξινομεί αυτόματα σύμφωνα με την τιμή των δεδομένων δοκιμών.
Βήμα 8: Συσκευασία
Μετά τις προηγούμενες διεργασίες, το δίσκο θα σχηματίσει τετράγωνα τσιπ ίσου μεγέθους (επίσης γνωστά ως "ενιαία τσιπ"). Το επόμενο πράγμα που πρέπει να κάνετε είναι να αποκτήσετε μεμονωμένες μάρκες με κοπή. Τα πρόσφατα κομμένα τσιπ είναι πολύ εύθραυστα και δεν μπορούν να ανταλλάξουν ηλεκτρικά σήματα, επομένως πρέπει να επεξεργαστούν ξεχωριστά. Αυτή η διαδικασία είναι η συσκευασία, η οποία περιλαμβάνει τη δημιουργία ενός προστατευτικού κελύφους έξω από το τσιπ ημιαγωγών και επιτρέποντάς τους να ανταλλάσσουν ηλεκτρικά σήματα με το εξωτερικό. Ολόκληρη η διαδικασία συσκευασίας χωρίζεται σε πέντε βήματα, δηλαδή το πριονάκι, το συνημμένο ενιαίο τσιπ, τη διασύνδεση, τη χύτευση και τη δοκιμή συσκευασίας.
01 πριόνισμα
Προκειμένου να κόψουμε αμέτρητα πυκνά διατεταγμένα τσιπ από το δίσκο, πρέπει πρώτα να "αλέθουμε" το πίσω μέρος του δίσκου μέχρι το πάχος του να ανταποκριθεί στις ανάγκες της διαδικασίας συσκευασίας. Μετά την άλεση, μπορούμε να κόψουμε τη γραμμή γραφής στο δίσκο μέχρι να διαχωριστεί το τσιπ ημιαγωγών.
Υπάρχουν τρεις τύποι τεχνολογίας πριονιστηρίων: κοπής λεπίδων, κοπής λέιζερ και κοπής πλάσματος. Η λεπίδα είναι η χρήση μιας λεπίδας διαμαντιών για να κόψετε το δίσκο, το οποίο είναι επιρρεπές σε θερμότητα και συντρίμμια τριβής και έτσι βλάπτει το δίσκο. Το DiCing με λέιζερ έχει υψηλότερη ακρίβεια και μπορεί εύκολα να χειριστεί τα πλακίδια με λεπτό πάχος ή μικρή απόσταση γραμμής γραφής. Το DICING στο πλάσμα χρησιμοποιεί την αρχή της χάραξης στο πλάσμα, οπότε αυτή η τεχνολογία ισχύει επίσης ακόμη και αν η απόσταση της γραμμής γραφής είναι πολύ μικρή.
02 Συνημμένο ενιαίο δίσκο
Αφού διαχωριστούν όλα τα τσιπ από το δίσκο, πρέπει να επισυνάψουμε τα μεμονωμένα τσιπ (μεμονωμένα πλακίδια) στο υπόστρωμα (πλαίσιο μολύβδου). Η λειτουργία του υποστρώματος είναι να προστατεύει τα τσιπ ημιαγωγών και να τους επιτρέψει να ανταλλάσσουν ηλεκτρικά σήματα με εξωτερικά κυκλώματα. Τα υγρά ή στερεά συγκολλητικά ταινιών μπορούν να χρησιμοποιηθούν για την προσάρτηση των τσιπς.
03 διασύνδεση
Μετά την τοποθέτηση του τσιπ στο υπόστρωμα, πρέπει επίσης να συνδέσουμε τα σημεία επαφής των δύο για να επιτύχουμε ανταλλαγή ηλεκτρικών σήματος. Υπάρχουν δύο μέθοδοι σύνδεσης που μπορούν να χρησιμοποιηθούν σε αυτό το βήμα: συγκόλληση καλωδίων χρησιμοποιώντας λεπτές μεταλλικές καλώδια και συγκόλληση τσιπ χρησιμοποιώντας σφαιρικά χρυσά μπλοκ ή μπλοκ κασσίτερου. Η συγκόλληση καλωδίων είναι μια παραδοσιακή μέθοδος και η τεχνολογία συγκόλλησης τσιπ μπορεί να επιταχύνει την κατασκευή ημιαγωγών.
04 Χύτευση
Μετά την ολοκλήρωση της σύνδεσης του τσιπ ημιαγωγών, απαιτείται μια διαδικασία χύτευσης για να προσθέσετε ένα πακέτο στο εξωτερικό του τσιπ για την προστασία του ολοκληρωμένου κυκλώματος ημιαγωγού από εξωτερικές συνθήκες όπως η θερμοκρασία και η υγρασία. Αφού γίνει το καλούπι πακέτου όπως απαιτείται, πρέπει να βάλουμε το τσιπ ημιαγωγών και την εποξική ένωση χύτευσης (EMC) στο καλούπι και να το σφραγίσει. Το σφραγισμένο τσιπ είναι η τελική μορφή.
05 δοκιμή συσκευασίας
Οι μάρκες που έχουν ήδη έχει την τελική τους μορφή πρέπει επίσης να περάσουν την τελική δοκιμή ελαττωμάτων. Όλα τα τελικά τσιπ ημιαγωγών που εισέρχονται στην τελική δοκιμή έχουν τελειώσει τα τσιπ ημιαγωγών. Θα τοποθετηθούν στον εξοπλισμό δοκιμών και θα ορίσουν διαφορετικές συνθήκες, όπως τάση, θερμοκρασία και υγρασία για ηλεκτρικές, λειτουργικές και ταχύτητες. Τα αποτελέσματα αυτών των δοκιμών μπορούν να χρησιμοποιηθούν για την εξεύρεση ελαττωμάτων και τη βελτίωση της ποιότητας των προϊόντων και της αποτελεσματικότητας της παραγωγής.
Εξέλιξη της τεχνολογίας συσκευασίας
Καθώς μειώνεται το μέγεθος των τσιπ και οι απαιτήσεις απόδοσης, η συσκευασία έχει υποστεί πολλές τεχνολογικές καινοτομίες τα τελευταία χρόνια. Ορισμένες τεχνολογίες και λύσεις συσκευασίας με το μέλλον περιλαμβάνουν τη χρήση της εναπόθεσης για παραδοσιακές διαδικασίες back-end, όπως η συσκευασία των πλακιδίων (WLP).
Τι είναι η Advanced Packaging;
Η παραδοσιακή συσκευασία απαιτεί να κόβεται κάθε τσιπ από το δίσκο και να τοποθετηθεί σε καλούπι. Η συσκευασία σε επίπεδο πλακιδίων (WLP) είναι ένας τύπος προηγμένης τεχνολογίας συσκευασίας, η οποία αναφέρεται στην άμεση συσκευασία του τσιπ ακόμα στο δίσκο. Η διαδικασία του WLP είναι να συσκευάσει και να δοκιμάσει πρώτα και στη συνέχεια να διαχωρίσει όλα τα διαμορφωμένα τσιπ από το δίσκο ταυτόχρονα. Σε σύγκριση με την παραδοσιακή συσκευασία, το πλεονέκτημα του WLP είναι το χαμηλότερο κόστος παραγωγής.
Η προηγμένη συσκευασία μπορεί να χωριστεί σε συσκευασία 2D, συσκευασίες 2.5D και συσκευασία 3D.
Μικρότερη συσκευασία 2D
Όπως αναφέρθηκε προηγουμένως, ο κύριος σκοπός της διαδικασίας συσκευασίας περιλαμβάνει την αποστολή του σήματος του τσιπ ημιαγωγών προς τα έξω και τα χτυπήματα που σχηματίζονται στο δίσκο είναι τα σημεία επαφής για την αποστολή σημάτων εισόδου/εξόδου. Αυτά τα χτυπήματα χωρίζονται σε fan-in και fan-out. Το πρώην σχήμα ανεμιστήρα είναι μέσα στο τσιπ, και το τελευταίο σχήμα ανεμιστήρα είναι πέρα από το εύρος τσιπ. Ονομάζουμε το I/O SIGNAL εισόδου/εξόδου (είσοδος/έξοδος) και ο αριθμός της εισόδου/εξόδου ονομάζεται Count I/O. Ο αριθμός εισόδου/εξόδου είναι μια σημαντική βάση για τον προσδιορισμό της μεθόδου συσκευασίας. Εάν η μέτρηση I/O είναι χαμηλή, χρησιμοποιείται η συσκευασία ανεμιστήρα. Δεδομένου ότι το μέγεθος του τσιπ δεν αλλάζει πολύ μετά τη συσκευασία, αυτή η διαδικασία ονομάζεται επίσης συσκευασία συσκευασίας κλίμακας τσιπ (CSP) ή συσκευασίας κλίμακας τσιπ (WLCSP). Εάν η μέτρηση I/O είναι υψηλός, χρησιμοποιείται συνήθως συσκευασία ανεμιστήρων και απαιτούνται στρώματα αναδιανομής (RDLs) εκτός από τις προσκρούσεις για να ενεργοποιηθεί η δρομολόγηση σήματος. Πρόκειται για "συσκευασία σε επίπεδο πλακιδίων ανεμιστήρων (Fowlp)."
Συσκευασία 2.5D
Η τεχνολογία συσκευασίας 2.5D μπορεί να βάλει δύο ή περισσότερους τύπους τσιπ σε ένα μόνο πακέτο, επιτρέποντας τα σήματα να δρομολογούνται πλευρικά, γεγονός που μπορεί να αυξήσει το μέγεθος και την απόδοση του πακέτου. Η πιο ευρέως χρησιμοποιούμενη μέθοδος συσκευασίας 2.5D είναι η τοποθέτηση μνήμης και λογικών τσιπ σε ένα ενιαίο πακέτο μέσω ενός παρεμβαλλίου πυριτίου. Η συσκευασία 2.5D απαιτεί βασικές τεχνολογίες όπως VIAS μέσω Silicon (TSVs), μικροδιαβλήματα και RDLs Fine-Pitch.
3D συσκευασία
Η τεχνολογία συσκευασίας 3D μπορεί να βάλει δύο ή περισσότερους τύπους τσιπ σε ένα ενιαίο πακέτο, επιτρέποντας ταυτόχρονα να δρομολογούνται κατακόρυφα σήματα. Αυτή η τεχνολογία είναι κατάλληλη για μικρότερες και υψηλότερες τσιπ ημιαγωγών I/O. Το TSV μπορεί να χρησιμοποιηθεί για μάρκες με υψηλές μετρήσεις I/O και η συγκόλληση καλωδίων μπορεί να χρησιμοποιηθεί για μάρκες με χαμηλές μετρήσεις I/O και τελικά σχηματίζει ένα σύστημα σήματος στο οποίο τα τσιπ είναι διατεταγμένα κατακόρυφα. Οι βασικές τεχνολογίες που απαιτούνται για τη συσκευασία 3D περιλαμβάνουν την τεχνολογία TSV και Micro-Bump.
Μέχρι στιγμής, τα οκτώ βήματα της παραγωγής προϊόντων ημιαγωγών "Επεξεργασία πλακιδίων - Οξείδωση - Φωτολιθογραφία - Χαράπιση - Απομονία λεπτού φιλμ - Διασύνδεση - Δοκιμές - Συσκευασία" έχουν εισαχθεί πλήρως. Από την "άμμος" σε "μάρκες", η τεχνολογία ημιαγωγών εκτελεί μια πραγματική έκδοση του "Turning Stones in Gold".
Ο Vetek Semiconductor είναι επαγγελματίας κινεζικός κατασκευαστής τουΕπίστρωση καρβιδίου του ταντάλου, Επίστρωση καρβιδίου πυριτίου, Ειδικός γραφίτης, Κεραμικά καρβιδίου πυριτίουκαιΆλλα κεραμικά ημιαγωγών. Η Vetek Semiconductor δεσμεύεται να παρέχει προηγμένες λύσεις για διάφορα προϊόντα SIC για τη βιομηχανία ημιαγωγών.
Εάν ενδιαφέρεστε για τα παραπάνω προϊόντα, παρακαλούμε να επικοινωνήσετε απευθείας μαζί μας.
Mob: +86-180 6922 0752
Whatsapp: +86 180 6922 0752
Email: anny@veteksemi.com
+86-579-87223657
Wangda Road, οδός Ziyang, κομητεία Wuyi, πόλη Jinhua, επαρχία Zhejiang, Κίνα
Copyright © 2024 Vetek Semiconductor Technology Co., Ltd. Με επιφύλαξη παντός δικαιώματος.
Links | Sitemap | RSS | XML | Privacy Policy |